Article II 3/2024: HOW SAFE IS OUR PACKAGING? UNDERSTANDING POTENTIAL FOOD SAFETY HAZARDS IN PACKAGING
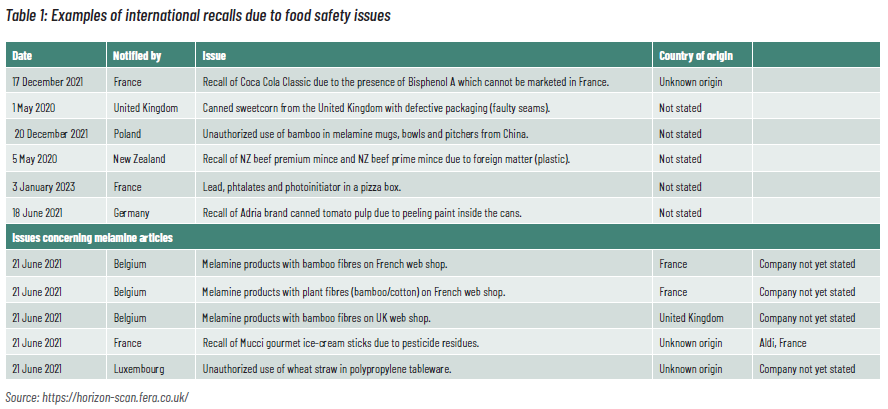
Packaging regulations
Some countries have more laws for a specific packaging component; for example, Swiss ordinances for inks and US Food and Drug Administration (FDA) for paper and board. However, in the United States of America (USA), each State has different requirements; for example, Californian regulations for per- and polyfluorinated substances (PFAS) are very different to the rest of the country; therefore, meeting the US FDA regulations is not enough. Similarly, different countries within the European Union have conflicting requirements, so just meeting EU regulations is also not enough. In the EU, all food contact materials have to comply with The Framework Regulation EU Dir No 1935/2004, and the Good Manufacturing Practice (GMP) Regulation No 2026/2006.
The following is a list of some of the world’s packaging manufacturing
regulations and relevant institutions:
• Legislation of individual EU Member States: details all the legislation that applies to food contact plastics in individual Member States http://ec.europa.eu/food/safety/docs/cs_fcm_non-harmonised.pdf
• The German BfR: https://bfr.ble.de/kse/faces/DBEmpfehlung_en.jsp?filter=clear
• The European Food Standards Agency (EFSA): http://www.efsa.europa.eu/
• In the USA, Chapter 21 Code of Federal Regulations (CFR) sections 170 to 199 contains a comprehensive body of legislation for a wide range of food contact materials from plastics through papers to adhesives.
• In the USA, USDA Approval codes: CFR 106 Infant formula QC Procedure, CFR 110 Current GMP in manufacturing, processing, packing or holding human food, CFR 175.300 resinous casings, CFR 178.3570 Industrial contact lubricants & CFR 178.3620 mineral oil.
• On April 19, 2023, the Chinese Food Safety Authority released the draft of the new version of GB 4806.1-2016 General Safety Requirements for Food Contact Materials and Articles, which is the most fundamental and general standard for Food Contact Materials (FCM) in China.
In Australia, environment ministers in June 2023 agreed to introduce mandatory packaging design obligations based on international best practice and to make industry responsible for the packaging they place on the market under a new regulatory scheme. They also agreed to regulate-out harmful chemicals and other contaminants in packaging.
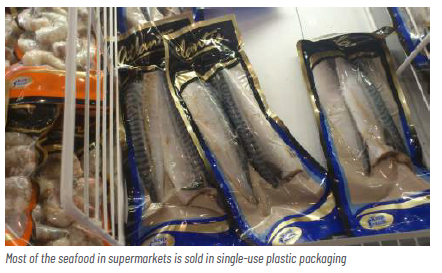
Reusable, recyclable or compostable packaging
• 13 April 2022: Woolworths in South Australia introduced compostable shopping bags. Woolworths Australia has removed around 800 tonnes of plastic from produce packaging since 2018. The retailer has committed to making 100% of its own brand packaging recyclable, compostable or reusable by the end of 2023.
• 1 July 2022: India has imposed a ban on single-use plastics to combat worsening pollution. This includes straws, cigarette packets, cutlery, earbuds, packaging films, plastic sticks for balloons, candy, and ice cream.
This means biodegradable packaging can be made from bio-based and fossil-based polymers, not just plant-based material. To be certified compostable, the packaging goes through rigorous testing, including being able to completely break down in 90 days in a commercial composting facility and 180 days in a home compost. Biodegradable packaging is generally defined as any form of packaging that will naturally disintegrate and decompose. To be biodegradable, the polymer structure (string of monomers) that make up the material must be able to disintegrate, or break down, into tiny pieces that can be safely digested by microorganisms.
Recycled plastics
Compostable packaging is made from a variety of plant-based materials, while recyclable packaging is made from previously used materials, including paper and plastic. The latter is processed at a recycling facility and made into something new to continue its circle of life. There are regulations with regard to recycled packaging manufacture in some countries but not all:
• Mechanically recycled Polyethylene Terephthalate (PET) can be approved by EFSA and US FDA.
• Other plastics can be sourced from chemically recycled products (Advanced recycling – Ending Plastic Waste (csiro.au).
• Post-Consumer Recycled (PCR) materials will need: sustainability declaration or delivery documentation to verify chain of custody, and a Declaration of Compliance or Statement of Compliance that spells out the EU or FDA approval.
• The FDA has some specific guidelines under which the use of recycled plastics in direct food contact can be acceptable (http://www.fda.gov/Food/GuidanceRegulation
G u i d a n c e D o c u m e n t s R e g u l a t o r y I n f o r m a t i o n /IngredientsAdditivesGRASPackaging/ucm120762.htm).
• Food manufacturers need a Declaration of Compliance for the final product from the plastic converter. This will include the regulations applicable to the recycled percentage of the resin/ film. Food contact recycled resins and films are extremely hard to source and are therefore at a premium price.
• The compliance will depend on the source (pre-or postconsumer recycle), material (PET, PE etc), recycling process (mechanical recycling, closed loop recycling) and the end-use market (EU, USA, China etc) for specific regulations to meet.
• Under EU current and draft legislation, chemical recycling involving complete depolymerization is exempt and subject to 10/2011. It is important to have a COC certification (Chain of Custody) like International Sustainability and Carbon Certification (ISSC) Plus or Global Recycled Standard (GRS) to prove traceability.
Plant-based materials
One of the key areas of development for sustainable packaging is plantbased
packaging, which can come in many forms:
• Hemp: Sourced from the cannabis plant, hemp is highly biodegradable, resilient and versatile. However, hemp is still an expensive source for bioplastics and not yet commercially available in its polymerized form.
• Paper: Paper is one of the oldest, traditional forms of compostable packaging. It biodegrades very rapidly and can easily and efficiently be recycled. The downside is that paper does not provide the same protection or sealing as other kinds
of packaging, so it may not be appropriate for a lot of food packaging.
• Polylactic acid (PLA): PLA is bio-based (plastic resin made from non-fossil resources) and can be moulded like conventional plastic into packaging; however, it is slowcomposting, even in an industrial composter. Some suppliers
have compost certifications for their resins/films, but there is currently no Australian recycling infrastructure.
• Cellulose: Plant-based packaging degrades very easily and is a great solution for short-term packaging, but it cannot provide shelf-life or a proper barrier for food products and it easily discolours when stored.
• Takeaway containers, napkins, cutlery, straws made from reclaimed and rapidly renewable sugarcane pulp.
• Bioplastic sourced from rapidly renewable plant resources, like corn. Ingeo™ PLA requires 52% less energy to produce and has a carbon footprint 71.8% lower compared to regular plastic.
• Seaweed: Like cellulose, seaweed-based material is highly biodegradable and great for short-term packaging, but is unstable and unsuitable for food packaging, transport and storage.
• Packaging could be the first major application of hemp bioplastics, a new study from Canadian researchers suggests. The research, by a team at Western University (WU), London, Ontario, replaced high-density polyethylene pellets used in conventional plastic with powder made by grinding up hemp stems. Tests showed that while the strength and malleability of the hemp-based material do not meet benchmarks in conventional plastics, it is nonetheless stronger and more malleable than other plant-based materials, while also being of sufficient quality for many applications.
Other aspects of plant-based packaging include:
• Active packaging that be a non-toxic insect repellent;
• Active packaging that has antibacterial compounds in the headspace, which can lead to taint in the food;
• The use of wheat starch (= gluten) in corrugated cardboard. The cutting of the corrugated cardboard makes dust which is likely to have gluten in it;
• Recycled cardboard gets “cooked” to over 200oC to kill pathogens but that doesn’t remove any residual allergens; and
• These active packaging options can be made of: citrus peel, cinnamon, neem, turmeric or pyrethrum extracts, essential oils or oleoresins. However, many of the listed plant sources are susceptible to food fraud i.e. cinnamon, neem and turmeric.
The European Commission and the EU Agri-Food Fraud Network published the results of a coordinated enforcement action on plastic food contact materials containing bamboo. After a year-long action there were 748 interventions (border rejection or recalls) leading to removal of affected products from the market. The addition of bamboo to plastic food contact materials can lead to the accelerated degradation of the plastic and leaching of formaldehyde and melamine.
Edible packaging
Dissolvable or edible packaging for food has emerged as a possible solution to some of the most challenging issues facing the sector today which include reduction of single-use plastics, packaging waste and the use of petroleum-based raw materials. These options include:
• Water-soluble (polyvinyl alcohol-based) edible film;
• Dissolvable food packaging which includes goods made with plant-based ingredients such as tapioca, seaweed and potato;
• Dissolvable food packaging to replace poly peanuts and bubble wrap made from prawn shells (chitin) which may lead to residual allergens;
• Spray-on food wrappers made from edible fibre (pullulan), which is a biodegradable polymer with a non-toxic solvent that can be rinsed off in water; and
• Food wraps made from fruit waste/by-products that are edible and compostable, that can replace single-use plastics.
There are no dedicated legal frameworks for dissolvable food packaging at present. In the US, edible packaging may be considered a food additive and would therefore require a Food Additive Petition (FAP) before it could be legally sold. In the EU, all food contact materials are covered by the harmonized legal framework Regulation (EC) No. 1935/2004. In accordance with Regulation (EC) No 1169/2011, it is also likely that the components of edible packaging will need to be included on a (food) product’s ingredients list. Additionally, customers can request further manufacturing requirements such as halal certification. These requirements include the following:
• No porcine-based products used; will need a statement;
• No alcohol-based products i.e. the inks, adhesives and solvents used;
• BSE/TSE controls: no bovine-based products; and
• Animal-based ingredients to look out for: tallow derivatives (resin formulations), fatty acids, esters and glycol.
Other equally important aspects to consider
• Designing packaging to survive the supply chain and to meet consumers' needs;
• The inadvertent inclusion of foreign objects from the packaging material;
• Packaging failure and waste;
• Migration of chemicals from the packaging material;
• Unexpected allergens in the packaging material;
• Bacterial survival in recycled materials;
• Legal compliance in all relevant jurisdictions;
• Loss of control of company-owned artwork;
• Validation of claims made by packaging manufacturers; and
• Rework/reuse/recycling of packaging.
When approving packaging, suppliers’ food manufacturers could consider the following aspects:
• GFSI certification for packaging manufacturers: BRCGS Packaging, SQF, FSSC 22 000 & IFS.
• Other certifications: ISO 9001 (this is only a quality management system, not food safety); HACCP (food safety hazard controls only); sustainability and responsibly-sourced i.e. FSC, ISCC & PEFC;
• Specifications including all “ingredients” used;
• Laboratory testing: for what? By whom?;
• Certificate of Conformance: to what?; and
• Validation of all claims: i.e. “Kraft” paper means “strong” as in the German meaning of the word, not the English. Paper products made this way are usually manufactured using sulphites i.e. they are not organic.
Moreover, each type of packaging has different aspects that need to be
considered beyond the usually supplied product specifications.
Considerations for paper products
• Is there pigment in the pulp?
• What is it coated with : wax- inside or out or both?
• Has the paper been recycled? if so at what percent?
• Has it been tested for residues i.e. chlorine dioxin?
• What is the geographical source of the paper pulp?
• What species of wood pulp has been used?
• What chemicals have the trees been treated with, e.g. arsenic?
Has the paper been tested for these?
• Has the paper been steamed, rolled or bleached?
• If steamed, has it been starched?
• If steamed, what is the source of the water and starch?
• If steamed, what is the boiler treatment used in the water supply?
• What chemical is used as a scale treatment in the water supply?
• Do they have a separate loop within the water cleaning system to avoid contamination from the chemicals?
• How and with what do they bleach the pulp?
• How and with what do they roll the paper, i.e. cross contamination?
Considerations for printed products
• Inks contain: resins (for stickiness), solvents (as coalesing agents), pigments, dyes, surfactants, biocides (usually waterbased) and defoamers.
• Pigment/dyes: (i) Are they foodsafe ? To what levels– FDA/ EU approved?; (ii) Have they been tested for heavy metals, i.e. lead?; (iii) Have the products being tested for chemical migration properties?; (iv) Are the inks the UV type that
have been cured using a photoinitiator like ITX (Isopropyl thioxanthone)?; and (v) If they have- do they have specific low migration properties ?.
Considerations for products with glues, laminates and wax
Glues contain solvents, biocides and surfactants and so need the following controls: (i) What levels are the residual monomers (these will smell like fibreglass if present)?; What is the Bisphenol A (BPA) content (linked to hormonal diseases)?; Can the BPA leach out ?
Laminates have similar issues as inks: are coatings used that contain Zonyl RP (flurotelomers) that can turn into Perfluorooctanoic acid (PFOA) which is a carcinogen ?
Wax coatings contain solvents, emulsions, biocides and sufactants: (i) What levels are the residual monomers (these will smell like fibreglass if present)?; (ii) What is the BPA content (linked to hormonal diseases)?; and (iii) Can the BPA leach out?.
Summary
Note: For more information with regard to food safety risks with packaging, book into the ICS training workshop https://training.integritycompliance. com.au/product/understanding-your-packaging-requirements/
References
https://australian.museum/blog/museullaneous/plastic-in-our-oceansis-killing-marine-mammals/
https://www.aljazeera.com/news/2022/7/1/india-bans-19-single-useplastic-items-to-combat-pollution
https://www.biopak.com/au/resources/what-is-pla
https://www.food.gov.uk/news-alerts/news/notice-to-retailers-plasticcontainers-or-utensils-containing-bamboo
Hemp can be substitute for polyethylene in packaging, Canadian study shows (hemptoday.net)
https://horizon-scan.fera.co.uk/
Intelligent & Active Packaging for Fruits & Vegetables edited by Charles.L.Wilson. ISBN 10: 0-8493-9166-0 https://www.pefc.org/
Recycled Plastic in Food Packaging: Perspectives in China, the United States, and the European Union | Keller and Heckman (khlaw.com)
Solutions for sustainable and deforestation free supply chains › ISCC System (iscc-system.org) https://fsc.org/en
https://tipa-corp.com/biodegradable-packaging/
https://www.woolworthsgroup.com.au/page/media/Latest_News/fruit-and-veg-shopping-gets-even-greener-as-woolworths-rolls-outcompostable-bags-in-sa/
https://www.worldwildlife.org/stories/whales-and-the-plastics-problem
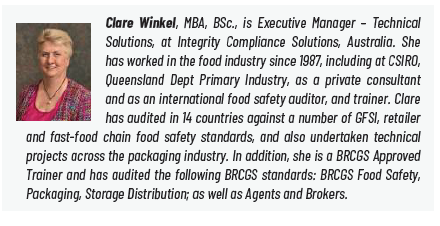